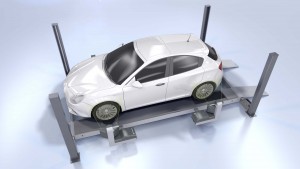
Wheel alignment used to be a complicated and time consuming task for workers in auto garages. Beissbarth, a Bosch company based in Munich is one of the pioneers in construction of wheel alignment systems of vehicles. Their system Beissbarth Touchless brings high-tech into the repair shop and by using machine vision and laser measurement; and it improves accuracy and speed of measurement. The system, however, took years of development together with project partners in the high-performance laser business.
Projecting a dot pattern
The overall machine vision system is developed in-house at Beissbarth and based on stereo 3D image acquisition and has four subsystems for each wheel to enable simultaneous measurement of all four wheels. Each of these four subsystems contains a laser that projects a precise dot pattern matrix over a projected area of about 80x120 cm covering the wheel and the surrounding environment such as the floor, chassis and the wheel case. The machine vision system takes reference out of the dot matrix which is projected onto the camera picture. The distance can be adjusted to up to one meter according to the car size. For a measurement process, the camera system detects the geometry of the wheel and its surroundings and the measurement function of the system uses the dot matrix generated by the laser.
One of the trickiest parts was the development of a laser source which fits to the requirements of the application. The projected dot pattern must have a very high depth of focus and must have an absolutely stable geometry; it needs to be bundled sharply at each possible working distance in order to be recognized by the camera.
This accounts in particular for areas on black rubber of the tire, which absorbs a lot of light. The entire system is calibrated by means of an elaborate process and needs to remain stable against aging or environmental influences such as temperature or humidity. Subsequently, the specifications of minimum and maximum size of each dot are very narrow and the requirements in the selection of a laser diode have been high. Here, Beissbarth partnered with German companies, one of them being Z-Laser.
Beissbarth has tested in long experimental runs of how the several thousand dot points have to shine at a minimum power in order to be analyzable for the machine vision system, this resulted in a very strong laser which is 4 to 5 times stronger than all Lasers which are standard for similar applications. The Laser applied here had to be on to upper limit of laser class 1M, in order to meet the balancing act between robustness and hazard-freeness. This meant a lot of effort in system design. “The laser diode we developed together with a partner is something rather unique and has a very high performance in the infrared wavelength range and an excellent beam characteristic”, explains Thomas Ruhnau, Head of R&D at Z-Laser. “The 1W single mode Laser source is quite symmetric and round, which is an important prerequisite. Diffractive optics creates 60x80 circular point dots with 150µW each. To be able to depict round dots the source must be point-like. Beyond that, the source is both longitudinally and transversely single mode with an M2 factor of 1.2 at most.” Through stress tests the consortium partners optimized and qualified the laser crystal used specifically to the requirements of the application. While the Laser chips are being produced by another project partner Z-Laser has jointly developed the structural design for the quality tests which also take place during production process. Here, the Laser chips are integrated into the system in the clean room in an automatic assembly and adjustment process, and sealed under protective gas atmosphere.
With the design of the industry product came the main requirement of safety, in particular for the eyes. Beissbarth developed and patented an enclosure with a glass pane, and uses a trick to ensure glass safety: Right before an actual laser beam is sent out for a measurement process, a test beam checks whether the safety glass is still unharmed and in place.
Having the laser source, it was up to the competence of the vision specialists at Beissbarth to create the suitable algorithms. “What is challenging here is the fact that the camera is looking at a rather wild environment with all kinds of components”, says Marco Kempin, Director Global Product Management Tire Service, Vehicle Alignment, Lifts, Test Lanes at Beissbarth. “There is the wheel, maybe the rim or a hubcap, parts of the chassis and the wheel house; there might even be a part of the garage floor on the picture.” Plus, size and structure of the wheels are different which each new inspected vehicle; even tires vary from balloon tires to ultra-high performance unflat tires. The puzzling part is to identify and filter out what is of interest. “Having only a limited number of points to analyze, the interaction of laser and software has to be perfect. So, besides an extraordinary laser, the algorithms lying behind the analysis are key to enable a robust performance.” The result is an accurate wheel alignment process in less than a minute.
Written by Andreas Breyer, Senior Editor, Novus Light Technologies Today