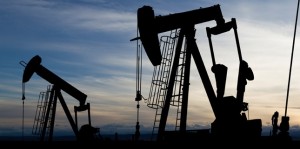
For years now, optical fibers have been used to sense temperature, acoustic and strain in oil & gas wells. As wells can be quite high in temperature, special coatings on the glass are necessary to ensure that the underlying glass remains protected throughout the life of the optical fiber. In telecom applications, a standard ultraviolet (UV) light cured coating is used and is rated to 85C. This coating is rarely used in oil & gas wells as the typical wells that are instrumented with optical fiber are at elevated temperatures.
As the temperature goes beyond 85C and up to 150C, the typical coating package offered is a layer of amorphous carbon over the glass that is a couple of hundred angstroms thick and then a UV cured high temperature acrylate. The carbon coating, which makes the fiber hermetic, is there to block the ingress of hydrogen into the glass, which would result in increased optical loss making the sensing measurements difficult to impossible. It starts to lose its ability to block hydrogen as the temperature goes beyond 150C and is fairly ineffective at temperatures in the 250C range. Note that above 150C, hydrogen protection methods are focused on the glass chemistry rather than using a carbon coating or other coating means to minimize the impact of hydrogen on the optic al performance of the fiber.
Coating during the draw tower process
Historically, getting a long length of the fiber coated properly so it was truly hermetic was a challenge, but over the past decade improvements have been made by some manufacturers that resolved these issues. Nevertheless, it is quite common to use carbon for applications above 150C as it does slow, but not stop, the ingress of hydrogen. It also provides fatigue resistance to the fiber, which can be an advantage, as it allows the fiber to survive mechanically at higher tensions than non-carbon coated fiber. Where this is important is if the fiber is coiled tightly, creating high bend strains or if the fiber is exposed to axial strain.
The optical fiber can be exposed to tight bends if the fiber is being coiled in an accelerometer for downhole seismic applications or simply in how the fiber is terminated. From an axial strain standpoint, for most downhole fiber optic sensing applications, the fiber is strain-free to ensure longevity of the fiber. There are applications such as pumping the fiber into a control line that can result in temporary elevated axial strain on the fiber. The carbon coating is a good precaution for this application to allow higher strain levels during the pumping process.
Thermal cured material for temps up to 300C
Above 150C up to 300C, the coating on the fiber is a thermal cured material called polyimide that is applied in several thin layers. Polyimide coating on optical fiber is ~15um’s thick – four times less thickness than the acrylate coatings used below 150C. It is notably tougher though, so the level of protection on the fiber is still reasonable. Polyimide is a challenging material to work with as its removal, typically for preparation for optical splicing, is notably harder than the acrylate coatings which are easily removed mechanically.
Hot sulfuric acid (120C) was the go-to method for years but it does create handling and disposal challenges. Another chemical that is used to remove polyimide is Dynasolve CU-7. It also needs to be heated and does take longer than other methods discussed here but has fewer drawbacks. Other means of removal of polyimide are using a plasma or electric arc to burn the material away, but this can lead to degradation in the strength of the glass fiber making subsequent handling more than difficult. Another method is to remove the polyimide mechanically with a razor blade. There is a commercial unit available that does this and subsequently tensions the fiber to ensure that the glass was not damaged in the process.
Another challenge of polyimide coated fibers is that it can become “sticky” at elevated temperatures. This is due to remaining solvent in the polyimide that was not “baked out” fully during the fiber manufacturing process. As the solvent migrates to the surface, it softens the outer-most layer and if severe enough, results in adjacent fibers sticking together in the cable or the fibers sticking to the inner wall of the metal tube that they are housed in. This phenomena is not necessarily uniform resulting in localized points of the fiber being fixed in place, which can and does result in high optical loss making the use of the optical fiber challenging if not impossible. Design and manufacturing enhancements by leaders in this market segment have been demonstrated to mitigate these issues over the past several years.
Beyond 300C
Beyond 300C, there are metal coated fibers with temperature ratings from 400C to 700C – aluminum, copper and gold – all quite expensive and difficult to get in reasonably long lengths. These fibers are used in fairly extreme enhanced oil recovery methods and other very small niche applications. Each type of metal coating has different capabilities, characteristics and challenges. If your application extends beyond 300C, it is best to consult the fiber manufacturer for guidance on the fibers and how best to handle and deploy them.
Optical fiber coating options, quality and performance have improved dramatically over the past 30+ years and continue to evolve allowing for new, creative sensing applications. When in doubt about what is possible, it is best to reach out to a specialty fiber manufacturer as they will have the most current knowledge of what is possible.
Written by Brian Herbst, Vice President of Sales for Fibercore